Features and benefits

Maximo in action
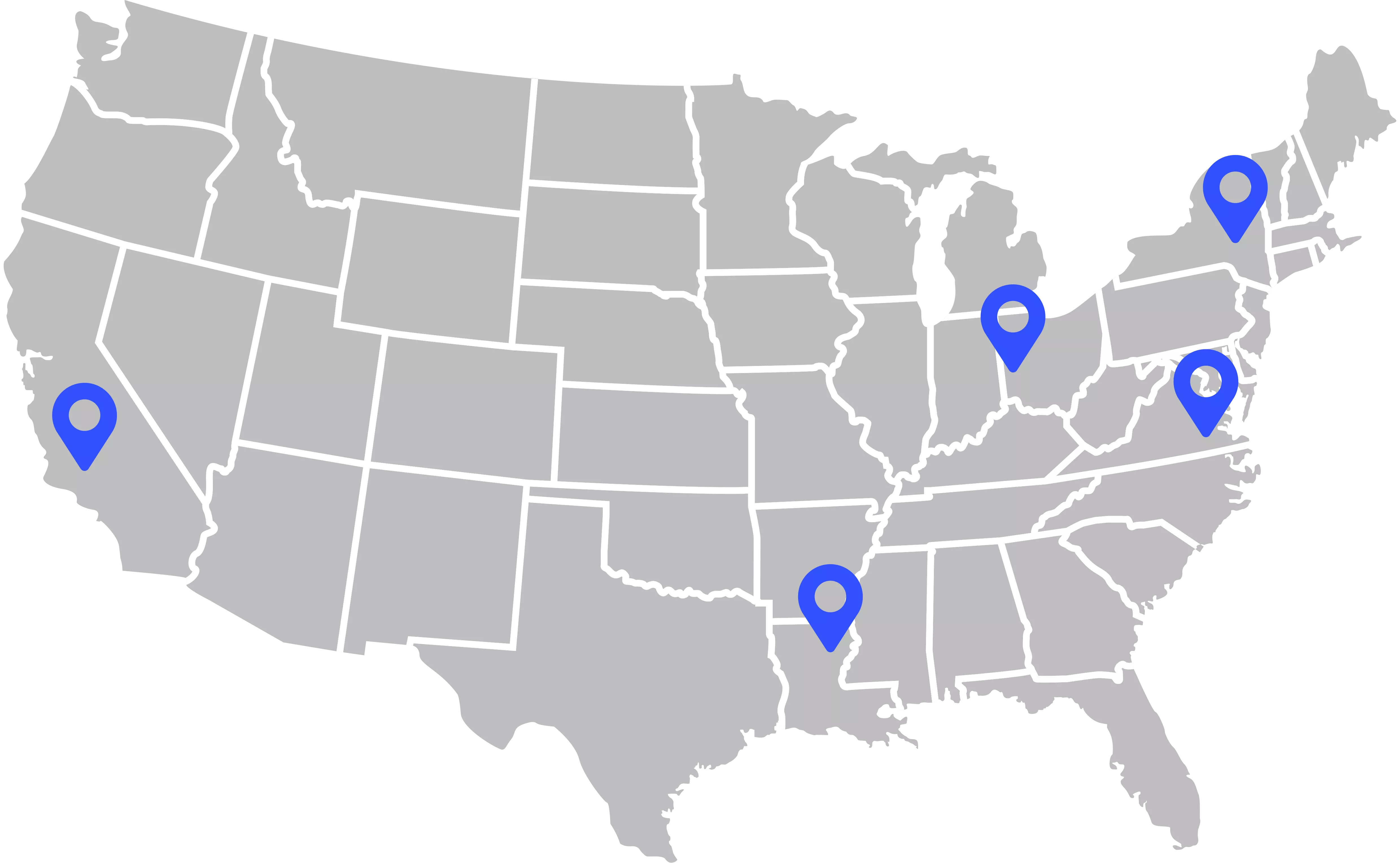
The making of Maximo
FAQs
Maximo is the only construction automation solution that provides the full end-to-end mechanical installation of solar modules directly in the field. The solar robot results in faster installation and creates safer working conditions, as construction teams do not need to lift heavy commercial solar panels – nor bend to place them – therefore reducing the risk of injury.
Maximo is technology agnostic to adapt to any solar module, and quickly expanding to a wide range of clamps, rails and trackers, which enables Maximo to install solar projects with single-axis trackers. Maximo tracks solar installation data, giving EPCs full visibility into their site's construction status.
Maximo works with solar construction teams to automate construction projects and install modules twice as fast as standard mechanical installation processes.
Maximo has been extensively tested and validated in a variety of conditions and job sites to ensure that it can perform in almost any weather condition, lighting condition, or terrain type.
It has successfully deployed nearly 10 megawatts of solar modules to date.
Yes, Maximo was built to sustainably operate in uncontrolled outdoor conditions.
Maximo runs on a mobile microgrid, using lithium-ion iron phosphate batteries as a power source. AC / DC inverters and phase converters supply the three-phase electric power required to run the larger components.
Maximo is equipped with a variety of controls and safety measures that allow it to work reliably in the field. The solar robot’s AI-enabled computer vision system detects any inconsistencies in the installation process and self-corrects to minimize any interruptions. The Maximo User Interface enables the operator to monitor the status of the Maximo unit, including the vision system and battery charge state.
Maximo combines a series of sensors, cameras, and advanced computer vision and artificial intelligence / neural network algorithms to identify the tracker structure, modules and other surroundings at solar construction projects, which serve as reference for the next module to be installed.
Advancements in computer vision, artificial intelligence and robotics have made it possible to automate tasks which just a few years ago would have been impossible to execute efficiently and cost-effectively. Applications of these advancements have been successful and are being increasingly adopted in other industries such as electronics, agriculture and automotives. In the solar industry, AI technology has been used to automate processes like preventative maintenance and module cleaning.
Solar panel boxes can be replenished with most skid steers or telehandlers, which easily lift a pallet of modules and load it into the module storage space through Maximo’s back panel.
Maximo is assisted by a human operator to move between rows on a solar construction site, and a skid steer driver tows the robot.
While we envision Maximo to have widespread use in every type of solar construction project that uses trackers , this system has great potential to solve problems in extreme desert conditions where working conditions are the hardest and where (in the US) installation jobs are harder to fill.
We also see a major benefit for solar module construction teams installing modules on the tallest trackers. Safety hazards surrounding working at heights lead to slower production rates. Maximo allows crews to install safely from the ground at the click of a button.
Site preparation: Staging and site preparation work are nearly identical to site prep and staging for traditional installation.
Maximo-specific preparation: Maximo is mechanically calibrated to ensure that its onboard systems are adjusted for the appropriate solar module and hardware used on the job site.
Maximo can be run by installation crews of two people. One person drives the system, and the other runs the machine and ensures everything is in place as the robot installs each row.
Maximo’s core robotics technology allows for the system to be positioned in a wide array of orientations and place each panel in the appropriate position. The system has tracks that enable it to maneuver on a variety of ground conditions, including in sandy, muddy, and bumpy environments.
Maximo works within the supply chain that exists today. We continue to work with module and tracker OEMs to integrate the latest technology as it is released. It is technology agnostic, adaptable to any solar module and quickly expanding to a wide range of clamps, rails and trackers. The Maximo team collaborates closely with tracker manufacturers to ensure seamless operations on current product offerings and to stay ahead of hardware revisions.